Kalamkari: A Tradition Continued and Renewed
March 23, 2021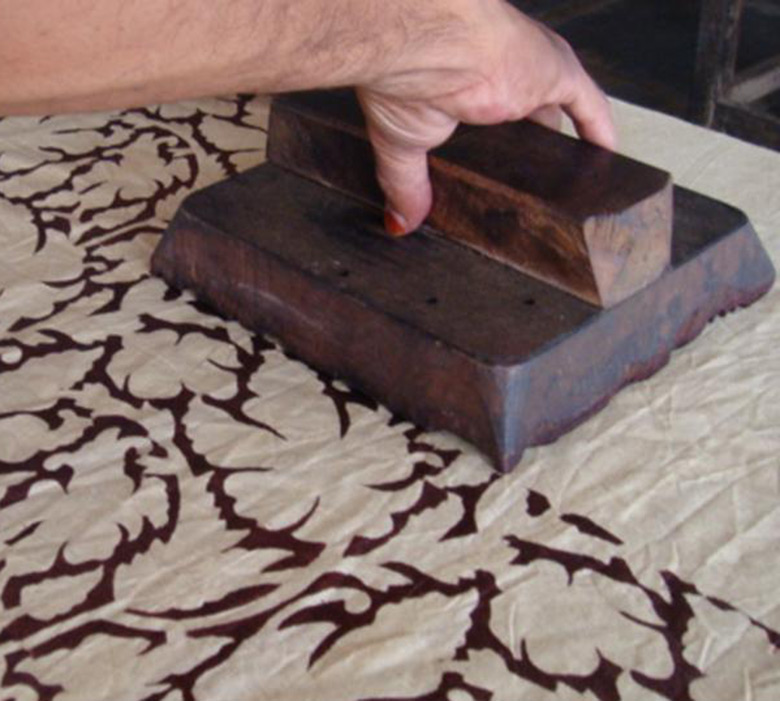
Kalamkari. Even the word, a mixture of Persian and Indian, reflects the storied past of this textile art. Kalamkari is an ancient Indian form of hand printing on cloth and kalamkari textiles were a prized trading commodity throughout Asia and Europe for hundreds of years. This traditional art has survived among dedicated artisans in southern India who follow the age-old techniques and natural dye recipes of this painstaking process.
MarketPlace is proud of its collection of beautiful and authentic Kalamkari fabrics. We work with the producers to create new and unique designs that still draw inspiration from the ornamental motifs developed through the centuries of trade. When you wear these remarkable garments, you are wearing a little piece of history!
Some of the natural dyes take days or weeks to prepare and are derived from a number of sources. Black dye is a fermented solution of rusted iron pieces and raw palm sugar. Red shades come from a long process involving pretreating with alum and boiling the cloth in a copper vat with roots and barks. Lime juice is used for pink.
In the first phase, several days are spent preparing the unbleached cotton with repeated washings, beatings and beachings.
Several more days are spent preparing the surface with myrobalam fruit and buffalo milk. Myrobalam seeds contain tannic acid, which acts as a mordant to set the dye, and the milk fat keeps dyes from spreading.
Subsequently mordants and dyestuffs are applied in specific sequences to produce the different colors, with more washings and bleachings in between.
After the fabric is treated, it is spread on a table that is slightly cushioned so that when the hand-carved wood block is pressed down, it makes an impression.
The wood blocks are a maximum of 6" squares and the precision of placing the block is extremely important so that the design does not look broken.
With Kalamkari, unlike batik, the fabric is never over-dyed. All parts of the pattern come from block printing with mordant. The background block is printed first and it is then filled in with different mordants and the color emerges when boiled. Because every color in a design is printed on, the precision is again of utmost importance. Notice the fine lines of the flower is printed after the larger outline and background has been printed.
Border blocks are narrower. Sometimes, depending on the design and width of the border, the artisan will use 3-5 different blocks to compose a border. The precision of borders is another challenge for the artisans. They are very skillful at mitering the corners.
An Alizerine solution is added to water in a copper pot and heated on a brick fireplace. Sometimes bark, leaves and dried flowers are added depending on the color needed. The mordant-printed fabric is then completely submerged, the cloth is swirled and boiled for over an hour. The length of boiling determines the intensity of the color needed. It is then dried again.
A lot of knowledge, skill, space, sunshine and water go into the production of beautiful Kalamkari fabrics.